Simulation Electrical Heating Water in Continuous Flow Mode
The simulation of electrical heating of water in a continuous flow mode can be performed with NOGRID points CFD software.
Directly electrically heated liquids are found in many industrial processes and apparatuses. In this case study, a continuously operated immersion heater is computed. Devices that provide a continuous supply of a heated liquid are also called water heaters or boilers or simply heat exchangers in the case of water. The immersion heater used in this study has an electrical resistance heating element enclosed in a container. The liquid to be heated flows through the container. The heating element is simulated as a separate solid and is in direct contact with the liquid. Due to the electrical resistance of the metal, the liquid is heated to varying degrees depending on the thickness distribution, geometry and position of the immersion heater. Since several materials are computed simultaneously in this simulation and are in contact, this is also referred to as a multi-phase simulation.
How NOGRID points software handles electrical heating of water
Based on the geometrical model which can either be imported from your CAD or created with our CAD preprocessor COMPASS you can generate a computer model of a specific geometry in a very short time (compared to mesh-based methods) and see its thermal characteristics in advance.
The following equation is used within NOGRID points to solve the electrical potential u in liquids and solids:
u electrical potential u = u (x, y, z)
σ electrical heat conductivity
q source term
In the field of electrostatics, the electrical potential does not change with time and the valid differential equation for the electrical potential u is the Poisson equation
Conduction in solids and liquids is described by Ohm's law, which states that current is proportional to the applied electric field. The current density (current per unit area) j in an area is directly proportional to the electric field E and the proportionality factor is the electric conductivity σ:
The electric field E can be calculated directly from the electric potential u by
The metal of the heater in this study is treated as a solid, i.e. only the temperature equation and the Poission equation for electrical potential are computed. The fluid within the chamber is of course in contact with the heater and heat can be exchanged, i.e. the temperature in the flow is affected by the temperature in the heater and vice versa. If, for example, the viscosity of the fluid depends on the temperature, then the temperature distribution of the heater has a direct influence on the flow in the nozzle.
The heat can be transferred either by heat conduction and/or heat radiation or by convection by means the flow of a fluid. You can couple also all kinds of heat transfer mechanisms. In the example ideal thermal contact between the nozzle and the fluid is specified.
Capabilities of NOGRID points CFD software
NOGRID points helps to understand the flow by visualization of the mass, momentum and heat transfer of single and multiple phases. You receive integral quantities which you can use to analyze the heat exchange efficiency. NOGRID unites abilities to handle free surface flow and moving parts in the domain and allows the simulation of any conceivable geometry and operation modes such as
- computation is in full 3D solving complete Navier-Stokes-Equations
- easy and intuitive setup also for FSI (Fluid-Structure-Interaction) cases
- free definable material properties by equations or curves,
- coupled solutions for electrical heating and fluid mechanic cases
- open or closed domains including inflow and outflow areas (non-batch mode)
- moving of parts and flexible thermal contact behaviour
Nogrid's strengths
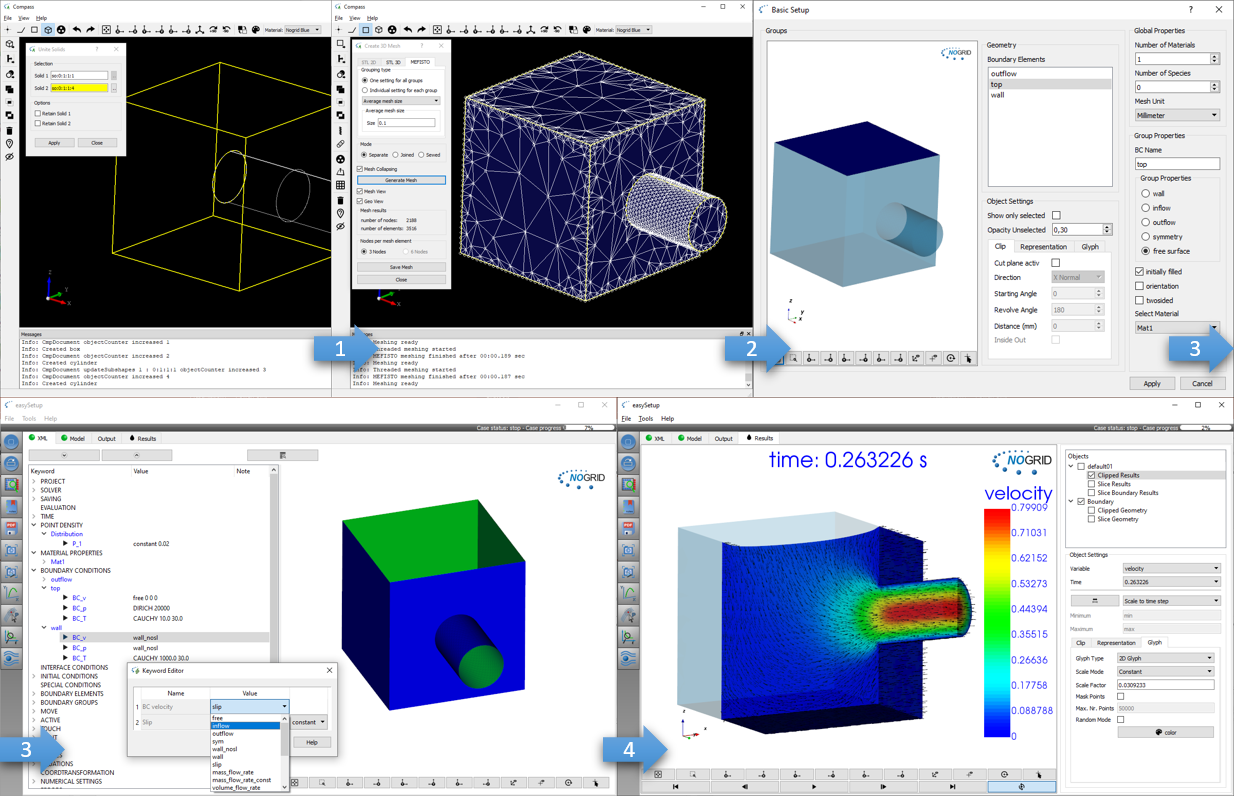
Easy and fast modelling: Build geometry, mesh boundary, setup the case and start computation
What is CFD from NOGRID?
CFD solves the fundamental equations that define the fluid flow process. With CFD software from NOGRID every engineer makes better decisions by predicting, analyzing and controlling fluid flow, heat and mass transfer or chemical reaction. By using NOGRID software for flow modeling you receive information on essential flow characteristics as for example flow distribution. Using it additional to testing and experimentation NOGRID software helps to improve the evaluation of your design – resulting in better construction and operation parameters, increasing planning security and money savings due to faster time to the marketplace for your product or process.
Choose NOGRID
With NOGRID, you choose professional CFD software and services – our aim is helping you to be successful. When you decide to work with NOGRID you choose close cooperation with a dynamic, flat hierarchies-organization. Short information channels result in quick and accurate professional support and service. Our team consists of highly qualified employees, who are experts in fields such as numerical simulation or computational fluid dynamics. Based on our know-how, we are pleased to offer the following services, responding to your individual requirements:
TRAINING
In our two-days training courses you will learn, how to use NOGRID CFD software efficiently. Our technical support team will teach you how to handle and solve different cases.
For more details please refer to Training Courses →
Technical Support
We offer full professional support from the minute you start using our software, by telephone or by email. Contact us, when ever needed.
For more details please refer to Software Support →
Service
Lack of time or resources and other constraints often make outsourcing an attractive solution. We help you with your flow modeling needs. Based on our engineering expertise in this field we offer individual numerical simulation services matching the unique needs of your organization.
For more details please refer to Simulation Services →