Simulation Flow Around a NACA 4415 Wing Model
At the Hochschule Karlsruhe, Germany, students tested a NACA model 4415 in a wind tunnel as part of a fluid mechanical lecture. The experiment was done for different approach angles of the NACA-model. The experiment was also simulated with CFD-tools such as NOGRID points. We outline the physical problem and results obtained by NOGRID points for an approach angle of 20°.
Physical model
The wind tunnel is modeled by a sufficiently large cuboid flow domain with "open" faces: Except for the inflow face the other five faces are outflow faces with a zero Dirichlet boundary condition for the pressure and zero Neumann boundary condition for the velocity. Using a "closed" box with only a small outflow area, opposite to the inflow area, would require a much larger fluid domain as otherwise the dynamic pressure would considerably increase.
At the inflow face the air flows in at 35.7 m/s in a circular area with a diameter of 0.35 m, outside the area the velocity is set to zero. This reflects the blast nozzle of the wind tunnel sufficiently well.
The faces of the NACA-model carry a wall slip condition. Compared to a noslip condition this yields much better numerical results as it avoids very large gradients of the velocity especially at the front of the model and it introduces only a small error.
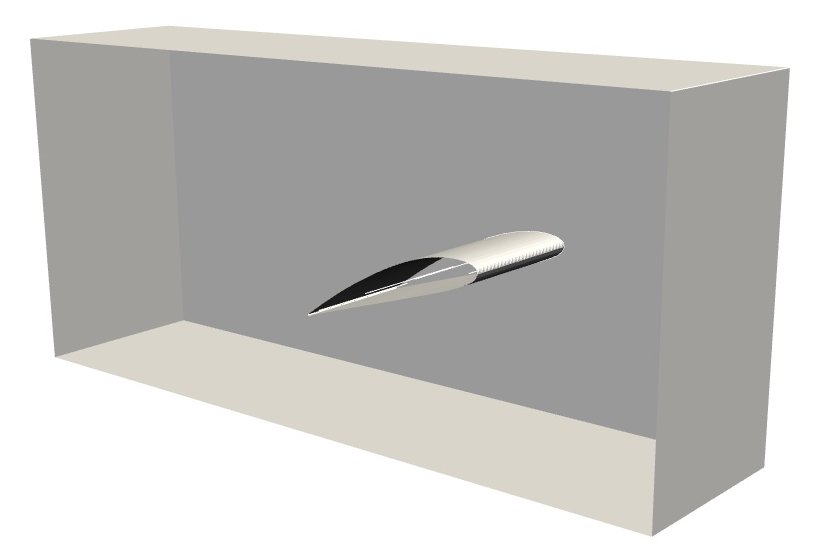
Figure 1: A cut through the cuboid flow domain with the NACA model, the inflow is at the right-hand side
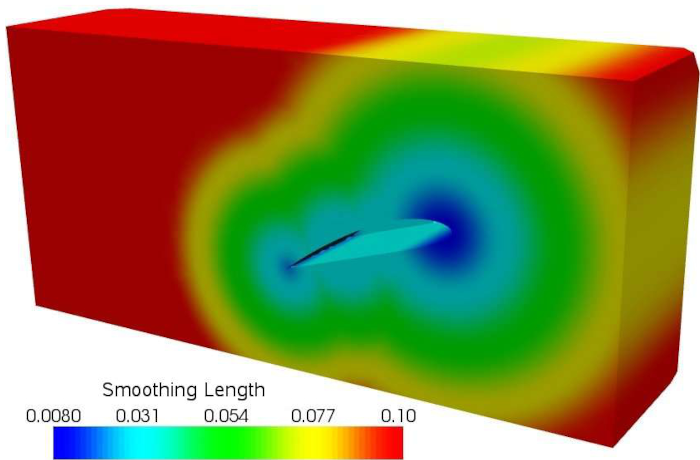
Figure 2: The smoothing length (which determines the point density) in the flow domain
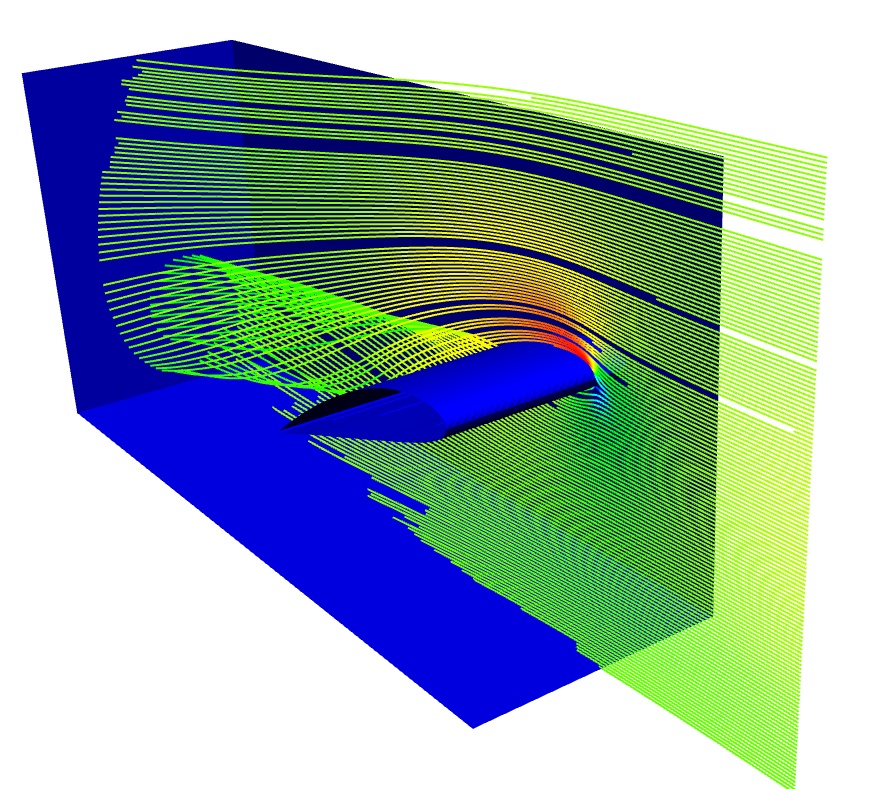
Figure 3: NACA model with stream traces
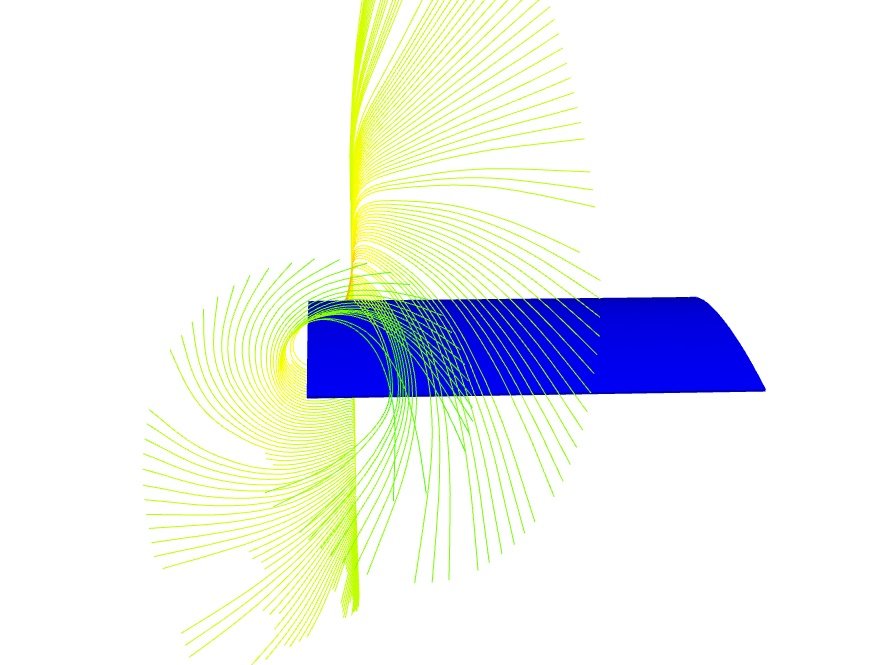
Figure 4: NACA model with stream traces seen from behind the model
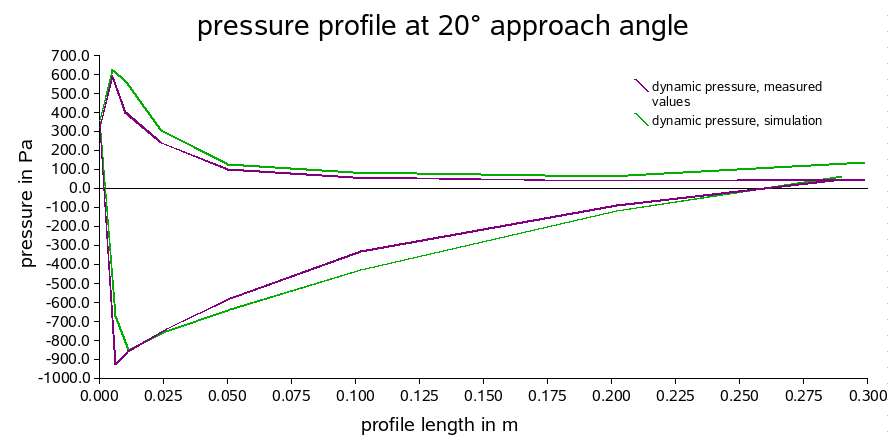
Figure 5: Comparison of experiment and simulation
In this case study we computed the air flow around a NACA wing. The preprocessing requires no volume mesh generation and therefore the modelling part is very easy. The User can therefore start importing the model directly and choose the smoothing length distribution, which effectively determines the density of points for the computation. As we are interested in the pressure profile at the surface of the NACA model we increase the density around the model. The high pressure gradient at the front of the model and the thinness at the back require an even higher density (or equivalently a smaller smoothing length). The distribution is shown in figure 2.
Comparison of experiment and simulation
In figure 3 and 4 path integration yields stream traces, which show the typical wake vortex generated by the positive and negative dynamic pressure below and above the NACA-model, respectively.
In order to verify the simulation quantitatively as well, the measured pressure profile along the surface of the NACA-model is compared to the simulation. The experimental data and the simulation data are presented in figure 5. They show a very good agreement of the experiment and the simulation. The small differences are probably due to small simplifications in the model, such as the rather small fluid domain, the omission of the suspension gear of the model, and the simplified blast nozzle of the wind tunnel.
Capabilities of NOGRID points CFD software
NOGRID unites abilities to handle air flows and allows the simulation of any conceivable wing geometry and operation modes such as
- computation is in 2D, axis-symmetric or full 3D solving complete Navier-Stokes-Equations
- easy and intuitive setup of the air flow case
- free definable material properties by equations or curves for each fluid
- large wing geometries with small gaps or holes
- open or closed domains including moving of additional parts
- any material combination for the fluids and for the wing material (in case of heat transfer)
Stärken der Nogrid Software
Wie Sie im Bild unten sehen können, benötigt man für die Ränder der Geometrie nach wie vor ein Netz, damit die inneren finiten Punkte den Rand detektieren können. Die Ränder müssen also vernetzt werden und die finiten Punkte im Inneren werden während der Simulation automatisch generiert.
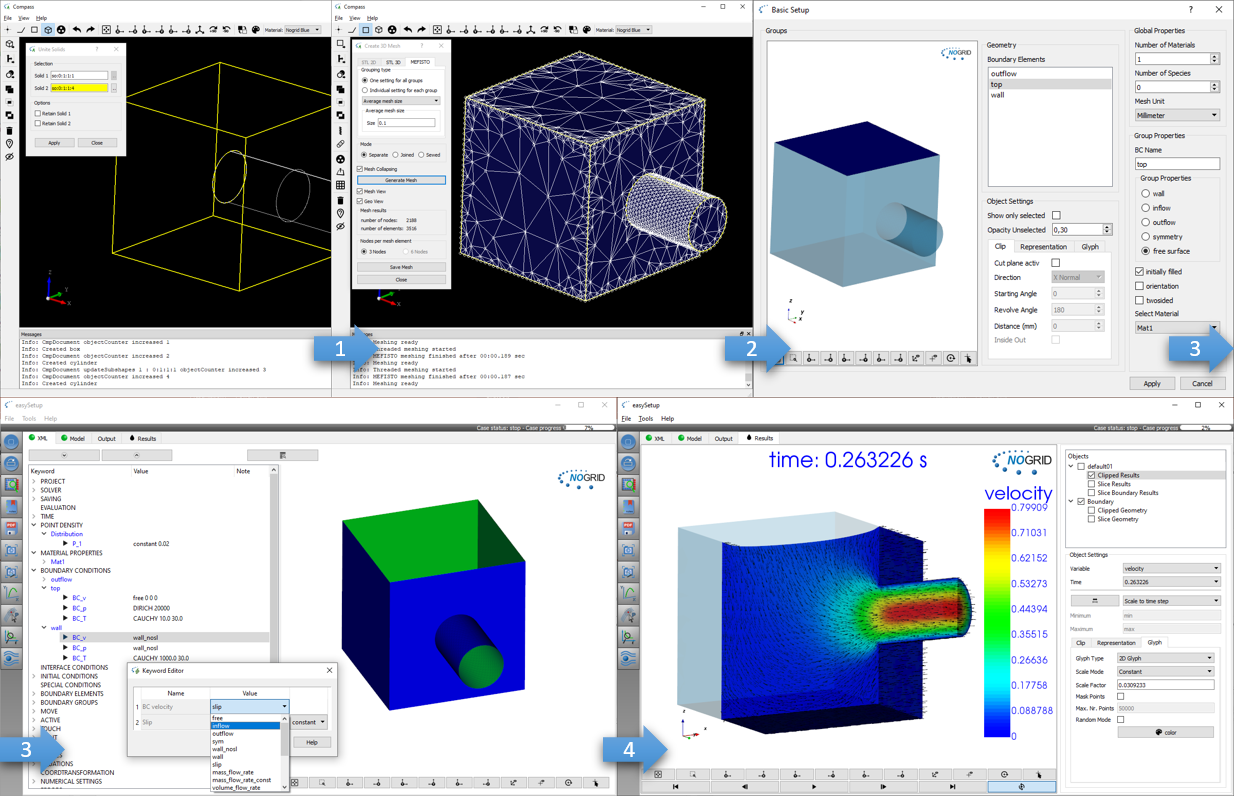
Einfache und schnelle Modellierung: Geometrie erzeugen und Ränder vernetzen, Fall aufsetzen und Simulation starten
Was kann die NOGRID Strömungssimulationssoftware für Sie tun?
Verlässliche industrielle Prozesse sprechen für sich und sind verantwortlich für den Erfolg eines Unternehmens. Für viele Prozesse spielt das Strömungsverhalten des Fluids eine wichtige Rolle für den Erfolg. Da industrielle Designs oft sehr komplex sind, gibt es verschiedene Faktoren, die in Fluidströmungs-Anwendungen wichtig sein können. Durch eine CFD-Simulation mit einer professionellen Software können Sie Ihre Prozessleistung simulieren und relevante Parameter berücksichtigen: Die Anwendung von NOGRIDs numerischer Strömungssimulationssoftware ermöglicht es Ihnen, die Fluidströmung, den Wärme- und Massenübergang sowie eventuell stattfindende chemische Reaktionen vorherzusagen, zu analysieren und zu kontrollieren und gibt Ihnen die Möglichkeit, Ihre Prozessleistung zu optimieren. Dadurch erhalten Sie eine Basis für bessere Design-Entscheidungen.
Die Strömungssimulationssoftware von NOGRID ist ein gitterfreies Tool mit erstaunlicher Flexibilität, Genauigkeit, Zuverlässigkeit und Robustheit. Die Software liefert qualitativ hochwertige Ergebnisse für ein weites Feld von Fluidströmungs-Anwendungen.
Warum sollten Sie sich für NOGRID Strömungssimulationssoftware entscheiden?
Zusätzlich zum Testen und Experimentieren hilft die NOGRID Strömungssimulationssoftware, die Bewertung Ihres Designs zu verbessern und den Erfolg Ihres industriellen Prozesses zu steigern. Zu lernen, wie sich die Fluidströmung verhalten wird und wie sicher industrielle Prozesse oder Prozessschritte funktionieren, lässt Ihr Wissen von Simulation zu Simulation wachsen. Sie bekommen ein besseres Verständnis für Ihre Prozesse, was wiederum zu enormen Einsparungen von Herstellungskosten und - zeit und gleichzeitig zu einem Endprodukt von hoher Qualität führt. Durch Simulation erhalten Sie bessere Konstruktions- und Betriebsparameter, steigende Planungssicherheit und Sie sparen Zeit und Geld dadurch, dass Sie Ihr Produkt schneller auf den Markt bringen können.
Training
In unserem zwei-Tage Trainingskurs werden Sie lernen, wie man die NOGRID CFD/CAE Software effizient einsetzt. Unser technischer Support hat Erfahrungen in vielen Disziplinen und kann Ihnen zeigen, wie man schwierige Fälle bewertet, behandelt und löst.
Für mehr Details bitte hier weiterlesen: Trainingskurse →
Technischer Support
Wir bieten den kompletten technischen Software Support an. Von der ersten Minute an, ab der Sie die Software nutzen, können Sie uns über Telefon oder E-Mail erreichen. Schreiben Sie uns, wir sind Ihnen gerne behilflich.
Für mehr Details bitte hier weiterlesen: Software Support →
Service
Oft sind Zeit und Ressourcen knapp bemessen, so dass die Vergabe von Simulationsaufgaben eine attraktive Möglichkeit sein kann, um schnell und kostengünstig anstehende Aufgaben zu bearbeiten. Basierend auf unserem Know-how können wir eine Fülle von Serviceleistungen auf dem Gebiet der Simulation von Strömungen anbieten.
Wir modellieren und entwickeln für Sie. Sie brauchen hierfür keine NOGRID-Software Lizenz zu kaufen. Wir bieten Ihnen einen individuellen Berechnungsservice für Ihre Verfahren und Prozesse an, der genau auf Ihre Wünsche zugeschnitten ist.
Für mehr Details bitte hier weiterlesen: Simulation Services →